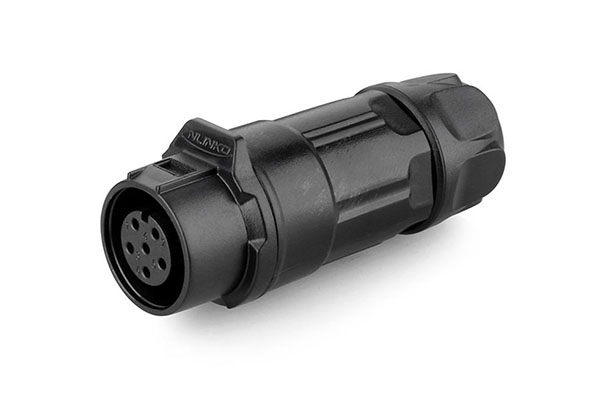
When it comes to industrial waterproof connectors, the current carrying capacity is a crucial parameter. People often inquire about this specification when purchasing waterproof connectors because it directly affects their usability.
What is the current carrying capacity of a connector?
It refers to the maximum current that a connector can handle without exceeding its highest rated temperature. It is important to note that the rated temperature includes both the conductor temperature rise and the ambient temperature. So, what factors influence the current carrying capacity of industrial waterproof connectors? Let’s explore this question in detail.
Factors Affecting Current Carrying Capacity:
Ambient Temperature and Connector Temperature Rise:
Temperature is a key factor that affects the current carrying capacity. It includes both the ambient temperature and the connector’s conductor temperature rise. If the temperature of the waterproof connector is too high and it doesn’t dissipate heat effectively, the current carrying capacity will be limited, affecting the reliability of the connector and potentially leading to safety hazards.
Conversely, when the ambient temperature is suitable and the connector has good conductivity and heat dissipation properties, the temperature consistency within the connector will be better, resulting in lower temperatures at the highest temperature point and enabling the connector to withstand higher current loads.
Contact Material and Surface Treatment:
The contact material of a waterproof connector should have higher conductivity and sufficient mechanical strength. Copper alloy materials are commonly used for contact components. The contact surface is usually treated with a metal protective layer, typically employing a surface treatment process that involves a nickel underlayer and a precious metal layer.
The nickel underlayer helps prevent potential degradation of the precious metal surface layer, while the precious metal provides good electrical and thermal conductivity. Using such materials and surface treatment significantly enhances the current carrying capacity of the connector.
Contact Geometry:
Optimizing the geometric dimensions of the contact components in waterproof connectors is essential. It involves designing the contact components with larger cross-sectional areas and shorter lengths within reasonable design limits. This ensures smaller overall resistance, thereby improving the current carrying capacity of the conductor.
Housing Material and Structure:
To enhance the heat dissipation efficiency of the connector, internal structural optimizations can be implemented in the housing design to facilitate internal convection. Furthermore, connectors with metal housings generally exhibit better heat dissipation than those with plastic housings. Effective heat dissipation allows for the design of contact components with higher current-carrying capabilities.
Conclusion:
Industrial waterproof connectors, such as the LP series and the award-winning BD M12 X connectors series by Shine Industry Electric, demonstrate excellent current carrying capacity. These connectors offer a wide range of connector types, one-handed operation convenience, excellent environmental adaptability, and interchangeable options between metal and plastic versions.
The BD series stands out with its visually striking streamlined body and hollow curved back design, exuding a sense of artistic aesthetics. On the other hand, the LP series features a simple and atmospheric design, showcasing understated elegance.
When selecting industrial waterproof connectors, considering factors such as temperature, contact material, geometry, and housing design is essential to ensure optimal current carrying capacity and reliable performance in various applications.